http://www.nceca.net/static/ documents/MalcolmDavis.pdf It's too bad that the slides that he used in the presentation are not available as well.
So here are some pictures of my Malcolm Davis Shinos - with and without Red Art. The one with Red Art is used on porcelain - with no Red Art you do not seem to get the orange colours on porcelain.
Since I use both B-mix - a porcelaneous stoneware and B-Mix for Wood Fire ( I presume it has something added to aid flashing) I tried both MD Shino with and without Red Art as I was not sure which one to use. In the gas kiln there seemed to be little difference between the two types on the above clays. However in the wood kiln the MD without Red Art seemed to get very little orange colour and the one with, seemed to go rather dark, more brown than orange. Maybe the ashes are washing out some of the orange? So not sure which MD Shino to use from now on.
![]() |
The Good: DH lithium slip sprayed on right and bottom as well as rim of bottle. Sprayed with Wirtz Shino and then poured on MD Shino on right shoulder. You can see how the lithium slips tends to bubble through. Same firing as above - in fact pots were next to each other. There was great carbon trapping where the shino was thicker due to the poured layer on the shoulder. Unfortunately this pot cracked on the bottom seam.
|
![]() | ||
The Good: Dark stoneware clay - one half poured with MD Shino with Red Art on left and the other half without Red Art. Waxed out design. Got great carbon trapping but no orange hues.
|
![]() |
The Ugly: MD Shino without Red Art - and without any lithium slip. Appliques were waxed out. Really ended up washed out. The ash deposit on the left removed what little orange blush that there was. I have to remember to take that into consideration when I load the kiln and make sure that the ash works with the design and not against it.
|
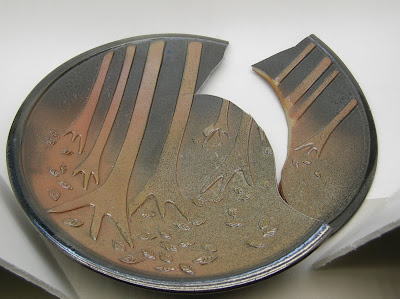
The Ugly: Lithium slip on top part and then wiped off the appliqued areas. Sprayed with MD Shino with Red Art - plate cracked but you can see that the orange on the left is not a vibrant colour. On the right there is quite a bit of ash deposit. Again the trees were waxed out, but no carbon trapping either.